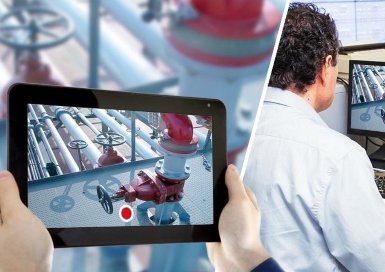
Many things have changed in the past few months and not all of them good as we have learned to cope with tragedy and a new way of living courtesy of the pandemic. COVID-19 certainly has a lot to answer for, but out of the situation that was forced upon the profession, a new way of surveying is fast emerging, particularly in the area of commercial ships and offshore assets. I refer to remote surveying, actually not new, but probably unimaginable to most of us just a few years ago; and a shock to the system of more traditional surveyors and those sceptics amongst us too undoubtedly. They are suddenly fashionable – the talk of the town it appears – and the pandemic has fuelled the latent demand for remote surveys.
Can a vessel really be successfully surveyed remotely? The answer is, of course, yes, but how detailed are remote surveys and what depth of information do they reveal to the surveyor who is watching on a laptop or tablet? I do not have the experience personally to be able to answer those rhetorical questions, but I know there will be IIMS members who can and who will fall on both sides of the debate. It would make for an interesting discussion. Whilst I can see the possibilities for commercial ship surveys, I remain more sceptical as to the surveying of yachts and small craft remotely. However, the fact that some of the ‘majors’ are seeing merit in remote surveying of larger vessels makes me think we must keep an open mind and take onboard their learnings and experience.
DNV GL reported back in March that they had completed over 15,000 remote surveys already. Obviously, they see the merit in working this way and the pandemic has driven their agenda.
So, do remote surveys mean the end of the marine surveyor? In my opinion, certainly not and far from it. But we are dealing with change on a major scale, the like of which has not been seen in the profession before. The role of the remote surveyor to look and interpret the data, report and make recommendations on what he or she sees is unchanged. But for many, I am certain being denied the opportunity to work in the open air and to get their hands dirty, surely some of the appeal of the job, will be sorely missed. Surely this outdoor freedom would disappear if the lot of a surveyor is to be sat endlessly at their electronic device observing remotely and then reporting? That has to be a game-changer. Perhaps it will encourage people from a different background to seek opportunities in the world of hi-tech remote marine surveying? Ultimately though, the surveyor must still understand what he or she is looking at or being shown through a smartphone screen. There can be no difference in that sense in terms of the required knowledge and experience. This means that the education of the next generation of marine surveyors remains the same, or does it? Those coming into the profession will need to learn new skills, apart from the ‘old fashioned’ technical ones, such as how to become an IT wizard, for that will become an essential part of the role. They will also need to understand the limitations of remote surveying if indeed there are any.
The Classification Societies have reported a massive uplift in the demand for remote surveys. This flies in the face of the fact that the industry has been relatively slow in adopting new digital technologies and to its detriment.
To spell it out simply, conducting remote surveys and inspections means that marine surveyors do not have to be physically present on board a vessel or marine asset. This dovetails perfectly, of course, with the social distancing requirements brought about by COVID-19. Instantly one can see the health benefits by not putting the surveyor, or indeed the crew, in a potentially harmful situation. Instead, by using an online connection or video streaming link, the remote surveyor can provide support to vessels anywhere in the world with documentation, images, video, and input provided by clients and crewmembers.
It is anticipated that remote inspection devices are likely to become commonplace in the future, even post-pandemic, replacing or assisting the physical attendance of surveyors. As previously stated, what we are dealing with is a seismic change that may well challenge those who are halfway through their careers, but which will become second nature to new entrants into the profession. They call it progress. Let’s now review what is going on amongst some of the Classification Societies as far as remote surveying is concerned.
Here is Lloyd’s Register’s (LR) current thinking on remote surveying.
The Classification Society has now undertaken hundreds of remote surveys, says LR Chief Surveyor, Iain Wilson, in a bold opening statement, with the “people who understand the technology pushing for it and using it.”
At present, a remote survey, which LR defines as a process without physical surveyor attendance, can be used for smaller tasks such as verifying a repair has been undertaken or ensuring minor damage has been rectified.
Wilson explains and accepts that while remote surveys aren’t always the answer to everything, they can ensure that there are fewer attendances on a vessel and a reduction in the number of interventions that may be required throughout the year. This is a huge advantage for owners and operators and has significant benefits for LR’s surveyors, he says.
A surveyor’s skill is rooted in analysing the collected data. Undertaking an inspection can be time-consuming and remote surveying techniques can facilitate a more efficient collection of data while allowing surveyors to focus their energies on the interpretation of the evidence, he explains.
Remote surveys can also spare a surveyor from the rigours of travel, eliminating the scheduling and safety risks from flying, driving, or a boat transfer that may be involved in getting an expert to the right location. Removing these travel uncertainties means that a 30-minute surveying job can be completed much more efficiently for all parties.
According to Wilson, a wide range of surveys can be managed through video and picture evidence using everyday technologies and he believes that the scope of remote surveys will continue to increase as the capabilities of the technologies increase and its cost-effectiveness is improved.
A remote survey may be appropriate when:
– The vessel is at sea when damage is sustained
– The vessel is at a port, terminal or location where the services of a surveyor are not available
– The location is remote, and no other surveys are due
– A minor statutory finding relates to the verification of documentation or the replacement of spare parts
– A Condition of Class (COC) relates to the verification of documentation or the replacement of spare parts
– The outstanding documentation can be readily verified using electronic communication
Surveys undertaken remotely are still viewed with caution by some, but experts at LR believe that reticence over new survey methods, which make the most of digital technology, is misplaced. James Forsdyke, LR’s Head of Product Management, and Sean van der Post, LR’s Global Offshore Business Manager, explain some of the reasons why the interaction between hardware, software and human expertise offers an unbeatable formula.
Restrictions on travel amid the COVID‑19 pandemic are forcing unprecedented change on some of shipping’s age‑old procedures as access to ships in ports, and oil and gas assets in offshore waters, is barred. Yet ships continue to fulfil a vital role in the global supply chain and energy facilities can’t easily be switched off. Both must continue to operate efficiently and safely whether surveys are due or not.
Nick Brown, LR’s Marine & Offshore Director, believes that the dramatic uptake of remote services and support is a trend that will inevitably continue, and likely gather pace, long after the virus. His sentiment is borne out by LR’s frontline experts – James Forsdyke, Head of Product Management, and Sean van der Post, Global Offshore Business Manager. Both experts agree wholeheartedly with Brown’s thinking. They highlight LR’s recent focus on remote services, notably its team of Remote Survey Champions located in no fewer than 16 of the world’s key shipping and offshore hubs. These experts can be linked digitally to their clients whenever necessary, and LR’s systems are ‘technologically agnostic’, meaning that connectivity can be based on Microsoft Teams, Skype or WhatsApp.
The team is interconnected by digital communications, real‑time data transfer, live streaming, and all of the other technologies that have been developed recently, but which the virus has now made essential. The remote survey champions are a hub of excellence who support and guide LR’s frontline colleagues and clients alike with remote surveys, ensuring consistent practices and safety at all times. Furthermore, Forsdyke believes that LR’s remote inspection techniques, combined with digital data transfer and the expertise of top specialists, can provide an equivalent service to physical attendance.
In times past, a traditional survey would involve a surveyor travelling to a location, going onboard a ship, meeting key personnel and then heading to the master’s office to check on the validity of certificates and other documents. It’s a process that could take a significant proportion of the available time. Then the surveyor would undertake the actual survey. Forsdyke compares this to modern banking applications, where you still need a whole range of valid documents before you can proceed, but now you upload all your documents in advance, for pre-validation, making the process infinitely more efficient. And he asks, ‘why can’t classification be the same?’
Far from reducing the role of the human being, Forsdyke says that latest techniques enhance it. LR’s experts in a particular field are instantly available to pass opinion on a specific issue, live‑streamed and on the scene. The client is receiving dramatically more added value from this service, he says, which is faster, more accurate, more incisive and no longer the result of one person’s physical attendance, often limited to a few hours.
Van der Post points to one recent development, forced on organisations like LR by COVID‑19, which amounts to a sea change. Previously, he says, no new procedure could be undertaken without detailed preparations, risk assessments and meticulous rules, written and prepared in advance. Safe working practices are, of course, essential, he says, but now the approach is “why can’t we do this remotely?” rather than “we must send someone as soon as possible”.
Both recognise the continued hesitance in the industry; as industry stakeholders collectively gain more experience of using remote techniques and demonstrate the capability, Forsdyke and Van der Post believe there will be continued acceleration of adoption and LR is poised to lead that sea change.
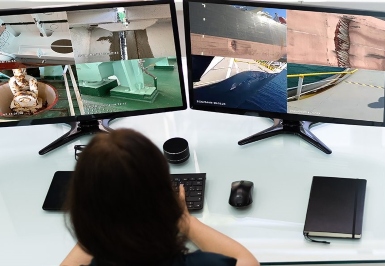
Moving on to RINA. Their website says that nowadays, one of the biggest economic challenges in every market is to avoid expensive travel when they are not really necessary. For some identified occasional surveys, RINA now provides a digital service for crediting such inspections remotely ensuring an equivalent reliability without the burden of time, money and resources. That sounds hugely compelling. So what types of remote surveys will RINA offer their clients?
The RINA web site is revealing. Currently, it says, the following surveys can be managed with remote survey techniques:
– Three months tail shaft survey extension
– Continuous Machinery Survey items
– Documentary verification
– Management of minor deficiencies
– Bottom inspection with ship afloat
– Radio Survey
– Survey for change of name
– Lay-up surveys
– Survey for change of load line
– ISM SMC-DOC audits
– ISPS ISSC audits
As further proof of acceptance, The Liberian International Ship & Corporate Registry has approved the use of RINA’s remote technology for inspections of Liberian-flagged vessels. It is anticipated that the decision by the Liberian Registry could shortly be followed by other flag administrations.
“The shipping industry is currently facing an unprecedented challenge and shoulders the responsibility of maintaining the flow of international trade during this crisis,” said Alfonso Castillero, COO of The Liberian International Ship & Corporate Registry.
“To ensure operational continuity, it is vital that we remain flexible and adjust our procedures in a way that protects personnel from exposure to the virus, while also increasing efficiency. RINA’s remote inspection technology facilitates the normal operation of our fleet by making vessel inspection completely accessible during a time when surveyor travel is near impossible.”
The American Bureau of Shipping (ABS), another Classification Society, has expanded and extended its remote survey options and has seen rising demand for these survey services. The company decided to expand its remote survey options for vessel owners and extend its remote survey and audit services for equipment and materials manufacturers and other key service provider firms.
“As organizations rely more heavily on remote and virtual operations, ABS is making it easier for vessel owners and equipment manufacturers to leverage digital applications by offering even more remote surveys and audit options,” Christopher J. Wiernicki, ABS Chairman, President and Chief Executive Officer, said.
ABS has expanded its remote offerings to include drydocking extensions and radio renewals and will offer additional remote services in the near future. Additionally, it has extended its remote survey and audit services to existing equipment manufacturing and external specialist clients enrolled in ABS programs in the United States, South America and Europe. According to ABS, access to remote surveys and audits allows for business continuity, particularly during challenging times that may create scheduling conflicts, personnel, or logistical issues such as the current COVID-19 period.
The Indian Register of Shipping (IRClass) has turned to remote surveys to maintain the validity of ships’ certificates and to support global trade, while ensuring the wellbeing and safety of staff. All of its office-based staff are now working remotely from their homes and the company has also provided specific guidelines to its surveyors to follow precautions and country-specific advisories when planning surveys.
IRClass says that due to COVID-19, some ships may experience operational challenges such as non-availability of drydocks, spares, or technicians. In addition, surveys and audits may, in some cases, not be conducted because surveyors are unable to attend the ships due to travel restrictions or quarantine.
IRClass is working closely with its clients and may also consider the postponement of non-critical work, where appropriate. However, where possible and with flag approval, IRClass is increasingly turning to the use of remote surveys and inspections. These are based on self-checks by the master/chief engineer of the vessel using the IRClass survey checklist and remote assessment of supporting documentation, photographs/videography by an IRClass surveyor. Facilities for video conferencing including live video streaming for viewing specific sections of the ship or equipment for cross verification, are also proving to be invaluable tools for IRClass’ surveyors.
The International Register of Shipping states that for remote surveys and inspections, the surveyors do not have to be physically present on board a vessel. As a result, they say, a remote survey can be conducted anywhere in the world without the surveyor’s physical presence. This also enhances survey flexibility and the efficiency of survey. Going on, they say a survey without attendance has benefits for both their customers and surveyors; however, safety must always be and remains their ultimate consideration and target. However, remote surveys will be permitted only for ships maintaining class with INTLREG.
The following surveys, which may be permitted using remote surveys techniques by the International Register of Shipping (INTLREG), are shown below. Such surveys could be subject to prior approval from the flag administration:
– Classification Surveys (annual)
– Condition of Class Surveys
– Minor damage and repair surveys for hull and machinery.
– Extension of Surveys (Class conditions, Propeller shaft, Boiler etc.)
– Continuous Surveys Machinery (CSM)
– Change of Owner, Change of vessel name / flag.
– A case by case approval
Suresh Sinha, Managing Director of IRClass said, “Our remote survey system is working very well indeed and is a practical and innovative way for our surveyors to carry out the emergency safety assessment of a ship around the various restrictions in place. Our surveyors can now deal with surveys, audits and inspections from the safety of their own homes subject to flag approval.”
“I can see remote inspections continuing to revolutionise classification services long after the COVID-19 outbreak using digital technology and real time, risk based, data driven decision making process – in not too distant a future,” he continued.
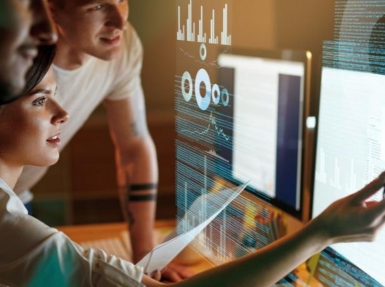
Bureau Veritas (BV) seems to have really caught the remote surveying bug and is running with it fast. In early February BV performed an engine test conducted jointly between Paris and a facility in China with multiple stakeholders witnessing the test process. A BV machinery expert located in Paris, the BV network office in Germany and an equipment maker in Europe were able to witness testing in a facility in China where BV surveyors were present.
Laurent Leblanc, Senior Vice President, Technical & Operations, BV, says, “This capability is really just starting to make an impact for our clients and stakeholders but we are well advanced in developing the necessary evolution to our rules, our procedures and connecting the remote survey technology with our digital platforms and tools.”
“Remote service delivery will become a part of everyday life for us. The capability does not replace our surveyors but allows speed of access and connectivity between teams and stakeholders to enable decisions to be made quickly and with confidence.”
Bureau Veritas Marine & Offshore has opened its first remote survey centre, located in the major maritime hub of Rotterdam. The centre is focussed on supporting remote service delivery capability and is part of BV’s North European Zone head office and BV’s Zone Marine Operations Centre.
Laurent Leblanc again says, “This is a new and important milestone in the Bureau Veritas global strategy of Digital Classification using digital technologies to transform the operating model of classification for the benefits of its clients.”
BV has conducted a full program of tests and proof of concepts confirming that the relevant technologies are now mature enough to enable remote surveys. Technologies used include optimised live-streaming solutions; connected devices (smart phones, tablets, Go-Pro cameras, smart glasses, augmented reality); and connectivity on board – with improvements from 4G networks and 5G yet to be realised.
Significant benefits to clients include speed of response and no travel or waiting time; optimisation in the decision-making process thanks to live-streaming solutions; continuous improvement in the quality of service; and cost control through overall reductions in travel time and arrangements.
Herman Spilker, vice president of the North Europe Zone for BV, commented: “The remote service delivery is led by a team of experienced surveyors and follows eight years of development experience. In 2012 we started developing the procedures allowing administrative verifications to be conducted remotely, Bureau Veritas is now able to offer a comprehensive range of survey items which can be performed remotely. The applicable survey items include classification surveys and specific statutory items which can be agreed by flag administrations.”
DNV GL reports it has seen a surge in remote surveys as vessel owners leverage the greater flexibility and efficiency they provide and the impact of the global COVID-19 crisis has reinforced the value of remote survey services. Remote surveys are not new for DNV GL with some 15,000 surveys and inspections undertaken since the launch in October 2018. DNV GL stresses the importance to their customers to continue to operate and deliver without disruptions to class services, and at the same time without compromising the safety of crews and surveyors. Remote surveys have provided the flexibility customers need, with global round the clock coverage, and improved efficiency through reduced travel times and increased availability.
“In these challenging times we are seeing the benefits of the full scope of digitalization initiatives that we have been building up over the past few years,” says Knut Ørbeck-Nilssen, CEO, DNV GL – Maritime. “The use of remote surveys has meant that we have been able to limit disruption to customer operations resulting from travel bans or quarantines involving our surveyors. Ship operators are able to receive immediately updated and verified electronic certificates, which make their business dealing with class, authorities and vendors much more efficient. This has all been backed by expert teams in the regions and through our DATE hubs, which cover technical and survey requests around the globe 24/7 and have solved 500,000 cases since the launch of the service five years ago.”
Remote surveys were first rolled out by DNV GL in October of 2018 and have been gaining in popularity ever since. In 2019, for some survey types, up to 25% of all surveys were conducted remotely, with more than one-third of customers having utilised the service at least once.
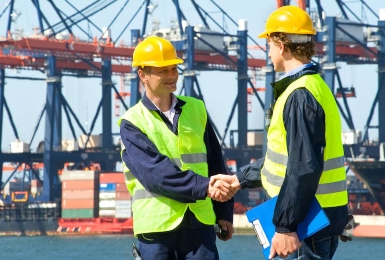
DNV GL says that with its new remote approach to machinery planned maintenance, Machinery Maintenance Connect (MMC), instead of requiring surveyors to travel to each individual vessel and go onboard, machinery data can be processed via algorithms and presented to customers on a digital dashboard. This enables the survey of a complete fleet in one process, while unlocking new insights into vessel and fleet performance.
“Once we have the verified data, to get going with MMC we sit down with management for an initial company audit that also functions as their annual survey,” says Rolf Petter Hancke, Surveyor and Principal Engineer at DNV GL. “This reduces the time required significantly, in one case we completed surveys on 49 vessels in roughly four hours, something that would normally take 50 separate onboard surveyor visits. And the data is all right there – easily and directly accessible by management in real time.”
So there you have it. Irrefutable evidence it would seem and like it or not, remote surveys are happening and are here to stay. A giant step for the marine surveying profession or fool’s gold? Let’s discuss and debate!
This article was authored by Mike Schwarz, Chief Executive Officer of the International Institute of Marine Surveying.
Links to other articles about remote surveys:
LR makes the case for remote surveys
DNV GL rolls out remote surveys for all vessels
RINA (Classification society) performs statutory and class surveys remotely
Bureau Veritas completes a remote marine survey on LNG dual fuel harbour tug PSA Aspen